A Tour of Maintenance, Repair, and Overhaul (MROs)Facilities by Katlin Edmunds
About the Author: Katlin Edmunds is a participant in IDB’s AIR-P Cohort 5. She shares her insights and knowledge gained during the MRO site visits in Salt Lake City, UT during Residency 2 of the Program.
The connection between, among, and within the MROs are an example of the benefits of collaborative efforts between the services. This was evident during this learning tour. Specifically the visit to Tooele Army Depot demonstrated the ability of an Army installation teaming with the private sector to showcase the collaboration and utilization of capacity that may have been underutilized in the past. It highlighted the organization’s commitment to relevancy.
This tour provided useful insights on the MRO functionality in the Western States both from both a commercial and government perspective.
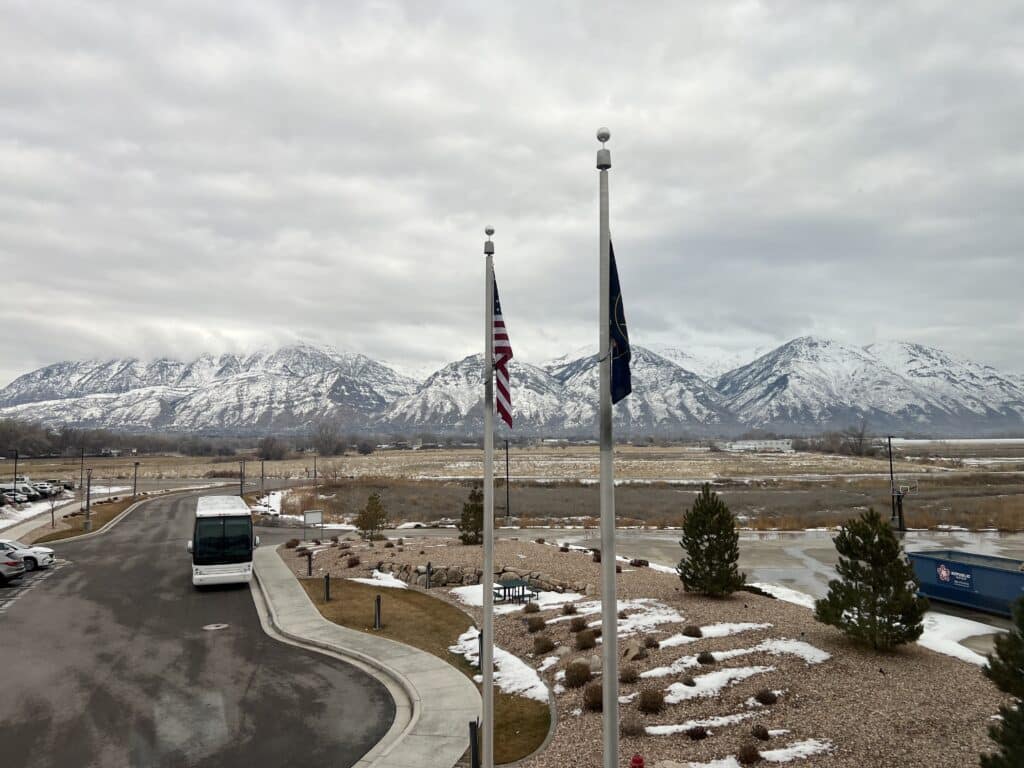
In January 2024, students in the Aviation Industrial Readiness Program Cohort 5 traveled to Salt Lake City, UT to witness Maintenance, Repair and Overhaul (affectionately called MRO) operations from both commercial and government facilities, specializing in both the aviation and ammunition spaces. As one of the only Army students in a class full of our Navy brethren, it was interesting to see the different perspectives the Naval Aviation community had vice the Army avionics and communications repair industry. We were able to tour the Northrop Grumman propulsion site on Monday morning where the facility specializes in Ammonium Perchlorate production which is used to power the propulsion systems of large munitions and rocket ships. Northrop Grumman purchased the facilities and operations from Orbital ATK in 2018 after receiving approval from the Federal Trade Commission. The Promontory, UT site had been in operation since the 1950s with a focus on providing exemplary propulsion support to Minuteman and Poseidon nuclear missiles, as well the Space Shuttle’s solid rocket boosters. The site included a vast array of testing facilities encompassing acres beyond our eyesight, and those test ranges were strategically designed to act almost like bunkers to absorb the shock of each rocket system testing event. It was clear that the sheer amount of engineering required to not only build the rocket motors but also construct a landscape for testing was quite impressive. The operations were clearly rooted in years of experience and understanding of how to preserve the beautiful Utah countryside.
The tour then stopped at a commercial MRO facility named Duncan in Provo, UT. This facility was a stark contrast to the operations we toured in the morning. This facility clearly wowed our group! We were thoroughly impressed from the moment we walked into this MRO operation because of two things, the passion of the employees and the cleanliness of the operations. When you think of MRO operations, you tend to think of a more particle filled environment, but this facility was almost as clean and open as a first-time production facility. The most impressive aspect to me was the way the organization could maximize space in the hanger to induct a variety of different sized and shaped aircraft for repair. Then, the facility also allowed for customers who brought aircraft in for service the opportunity to wait in a luxurious waiting room or wander through the facility to watch the repairs being conducted on the aircraft. What impressed us even more, aside from the videos of selling an aircraft off to Mr. Rick Ross and the amazingly impressively detailed artwork painted on the owner’s various aircrafts, was the passion and commitment you saw from the staff as they toured us through their operations. Clearly, the work conducted at Duncan demonstrated a sense of value to them, and it is why the company retains the founders’ name to this day.
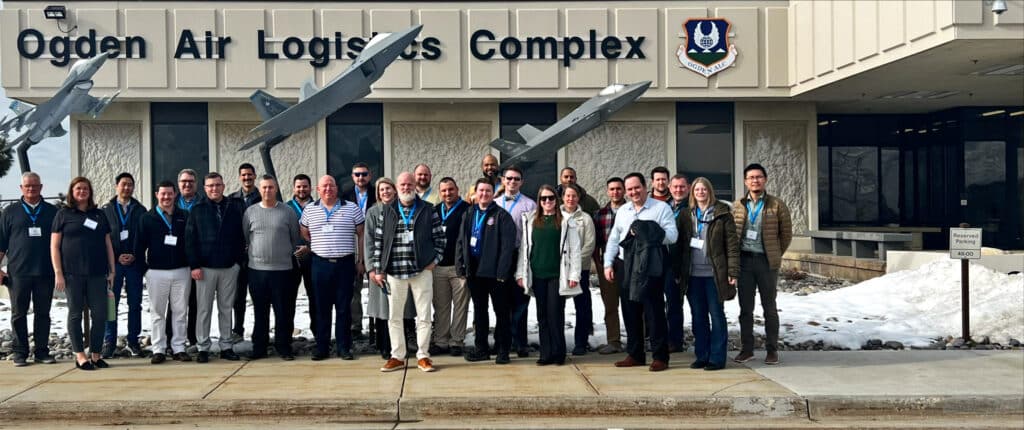
The second day of our stay in the Ogden Air Logistics Complex was focused on our ability to be independent thinkers to assist in value stream mapping four critical problems plaguing the complex, ranging from Defense Logistics Agency ordering process to the cyber infrastructure investment needed for plant equipment. These are not uncommon challenges facing an MRO operation in the government. It was interesting in working with the teams to discover that across the Air Force, the Navy, and the Army, we all face similar challenges but often do not have the appropriate network to benchmark each service on potential solutions. We found that continued collaboration and effective communication would benefit each of the groups in overcoming their constrained environments.
On our fourth day, we departed Hill Air Force Base and visited ES3 Solutions in Clearfield, UT. which focused on developing engineering solutions to solve aging infrastructure and equipment challenges for an aging fleet. It was apparent much of the talent located at ES3 had prior experience in the aviation industry, predominately working for Hill Air Force Base. Most of the workload at the installation was developed by taking a laboratory approach to solving plaguing issues for things from landing gear to fuselages. The main platform for service was the F-16, which is used by both the Air Force and Navy, so the fleet is larger, and the mechanical challenges are more pervasive across two services. This company focused on bridging that gap by developing solutions and then developing the methods for manufacturing and storage on a small-scale basis to support those platforms. The personnel at this organization were extremely passionate about the work being conducted and it was evident by the enthusiasm each demonstrated when briefing us and touring us throughout the facility.
As a nod to the Army, the group was able to tour the Tooele Army Depot! Toole Army Depot falls within the United States Army Joint Munitions Command located Tooele County, Utah. It serves as a storage site for war reserve and training ammunition. The depot stores, issues, receives, renovates, modifies, maintains and demilitarizes conventional munitions. The tour included a walk through of their machine shops that are used to manufacture certain piece parts in support of ammunition storage, specifically types of containers that could house different materials conducive for long term storage. The tour then took the group on a scenic drive across the installation, which was full of bunkers and other inground built armories, that brought us ultimately to the operations where Tooele Army Depot was executing the most successful Public Private Partnership the organization had experienced thus far. The intent was to demonstrate the ability of an Army installation teaming with the private sector to showcase the collaboration and utilization of capacity that may have been underutilized in the past. It highlighted the organization’s commitment to relevancy.
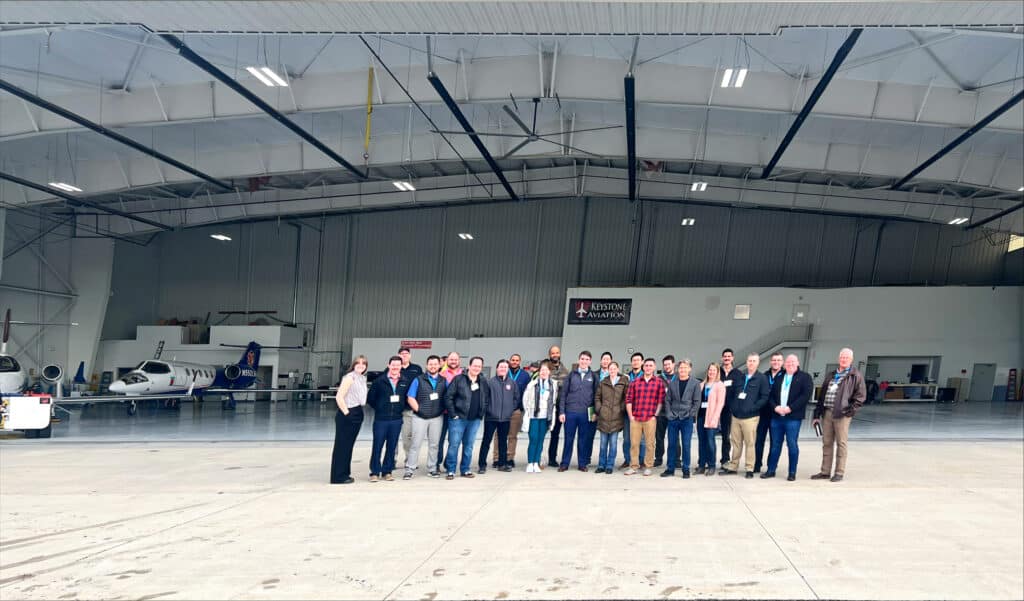
Our final stop was at Elevate MRO operations in Salt Lake City, UT. The facility was similar in nature to what the group toured at Duncan earlier in the week, but there were slight differences in the operations, from the cleanliness of the outfit, the capacity utilization methodology and the overall mixture of the operations. It was clear that Elevate focused solely on MRO operations and parts reclamation efforts, which are plaguing to the aircraft maintenance industry.
Overall the trip provided some useful insights for all students to walk away knowing more about the MRO functionality in the western states both from a commercial and government perspective. It is clear that MRO operations are a critical aspect of keeping equipment optimal, reliable, effective and operational, so any opportunities we have to broaden and expand our networks to benchmark best practices and gain a deeper appreciation of MRO challenges is a welcomed opportunity for all of us to take that knowledge back to our organizations and charge towards overcoming those challenges we may face, but never face alone!